Electronics Conformal Coating Market (2024-2035): Industry Analysis, Trends, and Future Outlook
Discover the latest trends, innovations, and growth opportunities in the Electronics Conformal Coating Market. Explore key drivers, challenges, and industry forecasts shaping the future of protective coatings for electronic components.
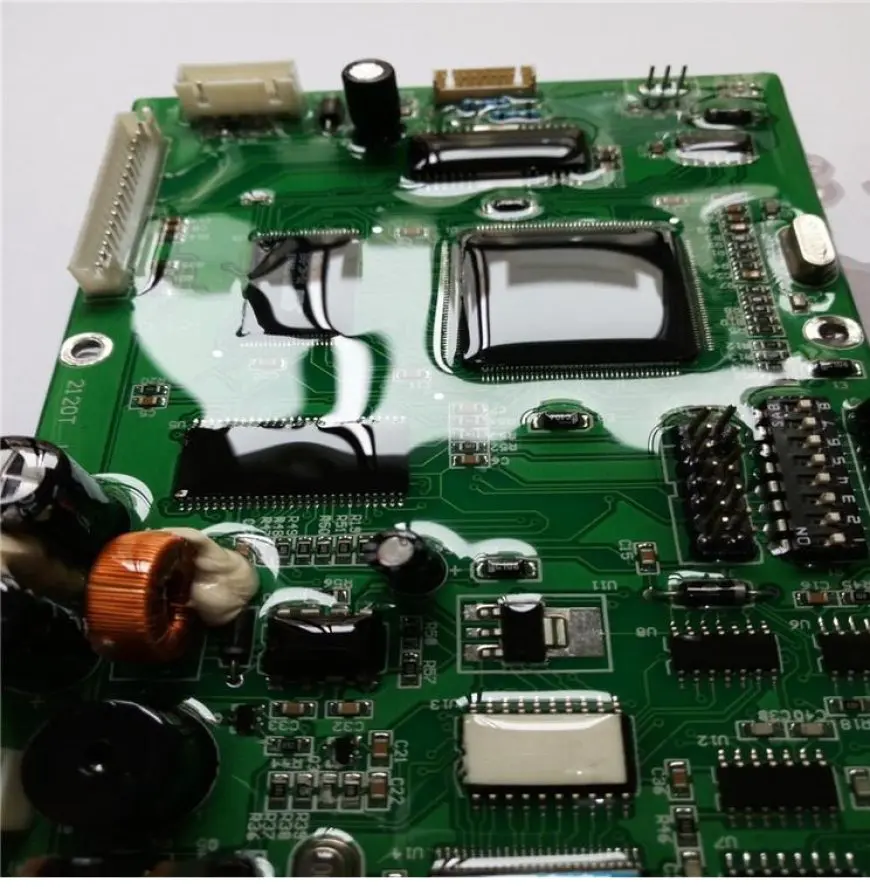
Market Overview
The global Electronics Conformal Coating Market is valued at USD 1.1 Billion in 2024 and is projected to reach a value of USD 2.29 Billion by 2035 at a CAGR (Compound Annual Growth Rate) of 6.95% between 2025 and 2035. The Electronics Conformal Coating Market is experiencing significant growth due to increasing demand for durable and reliable electronic components. Conformal coatings are protective materials applied to electronic circuit boards to safeguard them from environmental factors such as moisture, dust, chemicals, and temperature fluctuations. These coatings enhance the longevity and performance of electronics, making them crucial in industries such as automotive, consumer electronics, aerospace, and medical devices.
Common types of conformal coatings include acrylic, silicone, urethane, epoxy, and parylene. Each type offers unique advantages, with acrylic coatings being widely used due to their ease of application and cost-effectiveness. Meanwhile, parylene coatings are preferred for high-end applications due to their superior protective qualities.
Our comprehensive Electronics Conformal Coating Market report ready with the latest trends, growth opportunities, and strategic analysis- View Sample Report PDF
Key Market Trends
Increasing Demand for Miniaturized Electronics
The rapid development of wearable technology, IoT devices, and compact consumer electronics has fueled the need for highly effective conformal coatings. Miniaturized circuits require enhanced protection to maintain performance in smaller, high-density packaging.
Growth of the Automotive Electronics Sector
With the rise of electric vehicles (EVs) and advanced driver assistance systems (ADAS), automotive electronics require robust protection against harsh environments, including temperature extremes and vibration. This has driven demand for durable, heat-resistant conformal coatings.
Advancements in Coating Technologies
Recent advancements, such as nano-coatings and bio-based coatings, are reshaping the industry. Nano-coatings provide ultra-thin protection while offering superior moisture and dust resistance. Meanwhile, bio-based coatings align with growing environmental concerns and regulatory compliance.
Sustainability and Eco-Friendly Solutions
With stricter environmental regulations, manufacturers are focusing on low-VOC (volatile organic compound) and solvent-free coatings. Water-based and UV-curable coatings are gaining traction as sustainable alternatives.
Competitive Landscape
Leading Market Players
Key players in the electronics conformal coating market include:
- Illinois Tool Work (US)
- Henkel (Germany)
- Dow (US)
- H.B. Fuller (US)
- Shin-Etsu Chemical (Japan)
- Electrolube (UK)
- Dymax Corporation (US)
- Chase Corporation (US)
- Specialty Coating System (US)
- MG Chemical (Canada)
Take Action Now: Secure your Electronics Conformal Coating today – Purchase Now
Market Strategies
Leading companies are investing in R&D, acquisitions, and partnerships to expand their market presence. Many firms are also enhancing their product portfolios with sustainable and high-performance coatings to meet evolving customer needs.
Product or Service Analysis
Acrylic Conformal Coatings
- Pros: Easy application, quick drying, cost-effective.
- Cons: Moderate protection against chemicals.
- Applications: Consumer electronics, automotive electronics.
Silicone Conformal Coatings
- Pros: High-temperature resistance, flexible.
- Cons: Higher cost, longer curing time.
- Applications: Aerospace, industrial electronics.
Urethane (Polyurethane) Conformal Coatings
- Pros: Excellent chemical resistance, robust protection.
- Cons: Difficult to remove for repairs.
- Applications: Harsh environmental conditions, automotive electronics.
Epoxy Conformal Coatings
- Pros: Strong adhesion, chemical and moisture resistance.
- Cons: Brittle, challenging to rework.
- Applications: Industrial electronics, medical devices.
Parylene Conformal Coatings
- Pros: Superior protection, biocompatible.
- Cons: Expensive, complex application process.
- Applications: Medical devices, aerospace electronics.
Market Segmentation
By Type
- Acrylic
- Silicone
- Epoxy
- Urethane
- Parylene
By End-Use
- Consumer Electronics
- Automotive
- Aerospace & Defense
- Industrial
- Telecommunication
By Region
- North America
- Europe
- Asia Pacific
- Middle East & Africa
- Latin America
Pricing Trends
Pricing of conformal coatings varies based on material type, application complexity, and regulatory compliance. Historically, acrylic coatings have been the most affordable, while parylene coatings remain the most expensive. With the adoption of bio-based and nano-coatings, pricing is expected to increase due to the cost of advanced formulations.
Innovations and Developments
· Nano-Coatings: - Ultra-thin, high-performance coatings with enhanced water and chemical resistance.
· UV-Curable Coatings: - Fast-curing, low-VOC solutions improving production efficiency.
· Smart Coatings: - Integration of self-healing and conductive coatings for next-generation electronics.
· AI-Driven Quality Control: - AI-based inspection systems improving coating precision and efficiency.
Sustainability and Environmental Impact
Regulations Driving Change
Regulatory bodies such as REACH and RoHS are enforcing stricter guidelines, leading to lower VOC emissions and solvent-free formulations.
Water-Based & Bio-Based Coatings
Growing adoption of eco-friendly coatings to reduce environmental footprint.
Recycling and Waste Reduction
Manufacturers are developing recyclable coating materials to minimize industrial waste.
Case Studies and Data
Case Study 1: Adoption of Parylene Coatings in Medical Devices
A leading medical device manufacturer integrated parylene coatings into implantable devices, reducing failure rates by 30%.
Case Study 2: UV-Curable Coatings in Automotive Electronics
An automotive company reduced production time by 50% by switching to UV-curable conformal coatings.
For Electronics Conformal Coating Report and updates detailed: View Full Report Now!
Conclusion and Future Outlook
The Electronics Conformal Coating Market is set for substantial growth from 2024 to 2035, driven by increasing demand for miniaturized electronics, automotive advancements, and sustainability initiatives.
Key future trends include the rise of nano-coatings, AI-driven automation, and bio-based formulations. The market will witness increased adoption of environmentally friendly coatings, while innovations in smart and self-healing coatings will redefine industry standards.
Growth Opportunities:
- Expanding applications in wearable and medical electronics.
- Increased R&D investments in sustainable coatings.
- Adoption of AI and automation in coating processes.
As technology evolves, manufacturers must focus on innovation and sustainability to stay ahead in this dynamic market landscape.